The new wood gassification boiler should be here in a week or two. In the meantime we’ve been preparing the way by getting the old oil storage tank out of the way and installing a 650 gallon water storage tank from STSS, Inc. I’ve finally gotten my head around the design of the piping system and worked out the needed sizes and flow rates for everything.
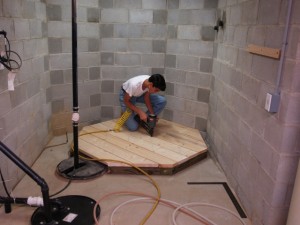
- Preparing a platform for the storage tank
A couple of unusual items, at least for a residential hydronic system, will be a 4 way flow control valve which is used to reverse the flow rate through the main heat exchangers in the tank, and a variable speed circulator which will be used to regulate the rate of heat transfer into and out of the tank in order to maximize the boiler operating efficiency. The latest piping diagram is here.
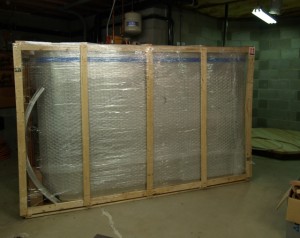
- Tank still in its shipping crate
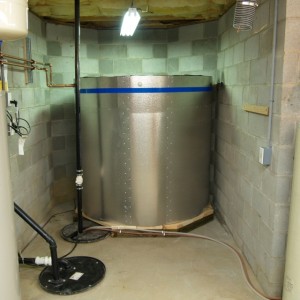
- Tank set up in place, no plumbing
So far the tank is sitting in place (empty of course), and the DHW heat exchanger has been connected already. We had to add a tempering valve to the INPUT of the DHW tank to keep it from overheating and to reduce efficiency losses. Leaving off the tempering valve might not be a bad idea in some cases though- a friend of mine who has a Hardy outdoor wood boiler and is heating DHW with it without benefit of a tempering valve finds that his daughters are not able to stay in the shower for a long time anymore since the rising water temperature drives them out!
System control strategy
With a rated output of 100,000btu, the EBW-100 boiler is able to deliver more heat than the house can consume (at the 1 degree F. design point, maximum heat input is calculated to be around 84809btu/hr, given the radiant piping plan and the flow rates chosen, with building total heat loss of 46770btu/hr). We don’t often see that kind of demand around here, though occasionally the temperature will drop below 0°F. The lower the heating demand on the boiler, the more heat will be available to charge up the tank. To maximize the efficiency of the boiler, it’s necessary to keep it operating continuously (no interruptions in forced combustion air) until the load of wood is consumed. Not only that, the water temperature should be kept around 160F, which is high enough to avoid condensation problems with flue gases, but low enough to ensure peak operating efficiency. Maximum boiler water temperature is 180F, whilst maximum storage tank water temperature is 170F due to its construction. In order to be able to transfer 100,000btu/hr continuously to the tank without the boiler getting ahead of it, we have to maintain a high volume of flow through the heat exchangers and try to limit the differential temperature from tank input to output to some reasonable amount. It turns out that a delta-T of about 20F at a flow rate of 10gpm is enough to maintain a transfer rate of 100,000btu/hr. As the tank temperature approaches 160F the boiler output will have to start backing down, since with the water temperature limit being 180F, the heat transfer rate to the tank will begin to decline as the delta-T will begin dropping below the 20F design setpoint. The circulator should be operating at maximum flow rate at this time in the cycle. Ideally, the load of wood should be almost completely burned off by the time the tank reaches 160F so that the boiler output can begin backing down just as the heat transfer rate from boiler to tank begins to decline. Ideally the boiler and tank would both reach steady state of around 170F at which point the tank circulator would shut off. The house zones would be used as a heat dump in the event the boiler temperature is still above 170F when the tank reaches this limit. As a last resort, the combustion air would be turned off, shutting down secondary combustion and damping the fire.
When the house is coming up to temperature and pulling heat out of the boiler, the tank has to be throttled back somehow to avoid overloading the boiler. As the house heating loops reach steady state, more heat will become available to transfer into the tank. Since a rather large circulator will be used for the tank loop, it seems inefficient to cycle it on and off to provide this control, since when the tank is cold and the house is taking heat, the ‘on’ cycles will be very short. Also, since we don’t need to take heat out of the tank nearly as fast as we put it in, it also seems wasteful to cycle the circulator as a means of reducing the rate of heat being drawn from the tank. It’s desirable to maintain the primary loop temperature no higher than that needed by the highest heating zone, currently about 130F, to minimize the rate of heat transfer needed from the tank. Taco makes variable speed circulators that will accomplish this control task very elegantly. A single 0011VV-IFC variable speed circulator with integral flow check should do the job nicely. Based on the hydraulic resistance curve of the tank loop we should be getting just over 10gpm when the pump is at full speed.
Note also we use a 4 way flow control valve to reverse the direction of fluid flow through the tank heat exchangers so that we always put heat in from the top (coolest water is fed to boiler return) and take heat out from the top (highest temperature water is fed to the primary loop). So it looks like the computer software is going to need some upgrading to do PID control of the tank circulator. More temperature sensors need added as well, as we monitor the temperature of the tank at the top, middle, and bottom to gauge the extent of heat stratification in the tank. With winter just around the corner it seems to make sense to defer installation of the solar collectors until next year, or when funds permit. Wood is starting to get a little more difficult to come by, seems everyone all of a sudden has decided that oil is no longer viable!